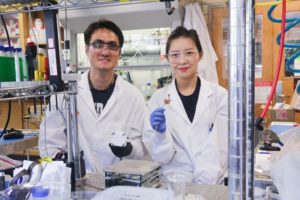
An improved catalyst designed by an international team of researchers — including many from U of T Engineering — increases both the stability and efficiency of a system that converts carbon dioxide (CO2) into valuable products such as fuels or plastic precursors.
“By using electricity to efficiently upgrade captured carbon into products we already use, we can improve the economics of carbon capture, and encourage investment in this emerging technology,” says Professor David Sinton (MIE), senior author on a paper recently published in Nature Catalysis.
“This new catalyst overcomes some of the key limitations that are holding back the performance of such systems.”
Sinton and his team use devices known as electrolyzers to drive forward chemical reactions that would not otherwise be energetically favourable. In this case, CO2 gas and a liquid electrolyte containing dissolved ions are supplied over a solid catalyst through which the electricity is supplied.
When the electrons combine with CO2 at the catalyst surface, they react to form carbon-containing molecules such as ethylene or ethanol. These molecules can be sold as fuels or commodity chemicals, and are precursors to many commonly used materials, from cosmetics to plastics.
The pH of the liquid electrolyte has a big impact on the system’s performance. For example, most of the previously reported systems operate under alkaline conditions, meaning high pH. While some of the CO2 pumped into these systems gets converted to the desired products, the vast majority of it reacts with the electrolyte itself to make carbonate salts, an undesirable side product.
In 2021, Sinton and his collaborators reported a new system that can operate under acidic conditions, meaning low pH. By making some changes to the chemistry of the electrolyte and the operating conditions of the electrolyzer, they were able to greatly reduce the formation of carbonate and increase the overall carbon efficiency.
However, those improvements came at a cost in terms of the stability of the catalyst.
“In that system, we added cations — positively-charged metal ions — to the solution, creating a thin region of alkaline conditions next to the catalyst surface, while leaving the rest of the solution acidic,” says Jianan Erick Huang (ECE PhD candidate), a co-lead author on the previous study and one of five co-lead authors on the team’s new paper.
“But in that region, which is only 50 micrometres thick, we still have the same problem as before: the formation of carbonate salts. Over time, these accumulate on the surface of the catalyst, and act as channels to bring in water molecules. Since the catalyst surface is designed to be hydrophobic, water destroys its reactivity.”
In their latest design, the team replaced the dissolved cations with an ionomer: an organic molecule that carries a positive electric charge. The molecule they chose is known as benzimidazolium, and the team applied a thin layer of it to the surface of their copper-based catalyst.
“Immobilizing the positively charged molecules on the surface of the catalyst prevents them from joining with carbonate ions to create salts,” says Dr. Mengyang Fan, a postdoctoral fellow in Sinton’s lab group and another co-lead author on the new paper.
“This made a big difference in terms of stability. While the old version of the catalyst only lasted about 12 hours, we measured the stability of the new one at more than 150 hours, which is more than 10 times as long.”
The change had the additional benefit of reducing another unwanted side reaction. In the previous system, about 30% of the electrons ended up producing hydrogen gas. This reaction siphons away electrons that would otherwise end up in the desired multi-carbon products, reducing the system’s efficiency. The new catalyst reduced this to less than 10%.
The system will still require further improvements before it can be applied at scale: for example, the stability of the catalyst will need to be further extended to many times its current duration. But the team believes that the new design points to a promising way forward.
“We did all this using a standard copper-based catalyst,” says Rui Kai (Ray) Miao (MIE PhD candidate), another co-lead author on the paper.
“There is a lot of experimentation that can still happen in terms of its chemical formulation, and there are other ionomers that could be explored. But this insight of a coating, as opposed to changing the chemistry of the solution, is a new insight, and we think it’s the way to go for future designs.”
– This story was originally published on the University of Toronto’s Faculty of Applied Science and Engineering News Site on August 21, 2023 by Tyler Irving.