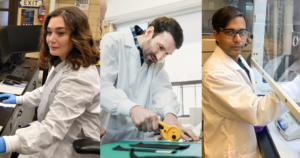
New U of T research by the DREAM laboratory, led by Professor Kevin Golovin (MIE), has developed a coating technique that prevents microplastic fibres (MPFs) from shedding during the wash cycle. These enhanced coatings adhere to synthetic fabrics and offer a solution to prevent 0.19 million tons of MPFs from contaminating the environment and water supplies yearly.
MPFs are primarily released from synthetic apparel, such as polyester or nylon clothing, and frequently end up in the washing machine, where they then drain into freshwater bodies and oceans. Abrasive friction between fabric and washing machine causes damage to individual textile fibres that break off and are released as MPFs. The ability of the coatings to lower the friction of synthetic apparel and prevent further damage is discussed in The DREAM laboratory’s new paper “Liquidlike, Low-Friction Polymer Brushes for Microfibre Release Prevention from Textiles” published in the journal Small.
“Our research shows that when the friction falls below a value around 0.25, microplastic fibres never form on the fabric and damage during washing is prevented,” says Golovin. “This low-friction strategy showed MPF reductions of up to 96% and gave the lab the opportunity to further refine what coatings work best to lower friction for each type of synthetic textile.”
Typically surfaces are lubricated to lower friction, such as with ball bearings or pistons, but the idea of lubricant-soaked clothing is not practical. Dr. Sudip Lahiri, a researcher in the DREAM laboratory and lead author of the study, had the idea to use “liquidlike” molecules, essentially lubricants that can be chemically bonded to fabrics.
“Liquidlike coatings have lower friction and can be strongly bonded to the surface of the fabric,” says Lahiri. “We successfully bonded one liquidlike molecule to nylon fabrics, and we wanted to extend the research to examine more coating options and additional synthetic fabrics, like polyester.”
Polyester and nylon fabrics account for approximately 90% of synthetic apparel produced. Scaling up these coatings has the potential to bring a positive shift in the textile industry and provide options for offering more environmentally friendly and durable materials to consumers.
“Recognizing the many different uses of synthetic fabrics, we expanded our research to provide different coatings that either wick water or repel it, but still drastically reduce the release of MPFs,” Golovin explains. “MPFs are released during washing, so durability to prevent the coating rubbing off in the laundry is essential, and also increases its effectiveness.”
Professor Golovin incorporated a two-layer fabric finishing strategy using a molecular primer and liquidlike molecules to minimize the release of MPFs even after repeated washes. The coated fabrics maintain other important parameters such as their softness and breathability, and some of the more promising ones are being scaled up for industrial adoption. The Natural Sciences & Engineering Research Council (NSERC) recently funded an Innovation 2 Ideas grant to do just that.
“We’re currently translating our lab-scale technology to a turnkey solution for the apparel industry thanks to a grant from NSERC, to reduce as many adoption barriers as possible,” explains Golovin. “Our goal is to provide a product that brands can start adopting by the end of 2024.”
-Published on April 22, 2024, by Kendra Hunter